Is it that time of year again already? Time to begin the tedious and lengthy process of taking your inventory? Of course, a periodic inventory system is just one option to stay on top of your inventory. But have you considered using a perpetual inventory system? You know, one that stays up to date automatically and eliminates a lot of the time-consuming tasks?
Well, if you haven’t considered which inventory management system you should be using, then you’ve come to the right place. We’re about to define perpetual inventory and explore the benefits and challenges of using this method.
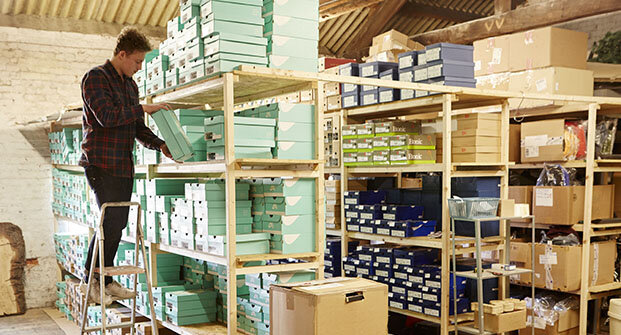
What is a perpetual inventory system?
A perpetual inventory system is an inventory method that updates your stock levels in real-time. Inventory tracking through the supply chain supplies automatic updates. The software monitors sales, deliveries, transfers, discarding, or any type of transaction.
Your warehouse and sales team members will typically scan inventory items as they come and go. The recording is either manual, via barcode, or radio frequency identification (RFID). The transactions become journal entries that update your inventory account.
Perpetual inventory system vs. Periodic inventory system: What’s the difference?
Perpetual inventory systems make a lot of sense to the modern business owner. But what did businesses do before we had the technology of today? Well, they all used some form of a periodic inventory system (or maybe nothing at all). Let’s take a look at a perpetual inventory system vs periodic and see how they stack up.
Unlike a perpetual inventory system, a periodic inventory system is not accurate and up-to-date in real-time. This is because the inventory records must come from physical inventory counts at regular intervals.
A small bricks-and-mortar retailer may opt to take stock levels every 3-6 months or maybe only once a year. While a busy online fashion retailer could need to count inventory levels at least once a month.
Image source: patriot
These physical counts are matched up against revenue to calculate the cost of goods sold (COGS) during an accounting period. This calculation is vital to help businesses determine their gross profit. So a beginning inventory and ending inventory are the minimum counts required.
However, with a perpetual inventory system, you will have your beginning and ending inventory available whenever needed.
The one benefit of periodic inventory systems is that they don’t incur any upfront costs on hardware and software. However, to make your life easier, you should at least consider retail accounting software for your record keeping.
A perpetual inventory system is built for e-commerce brands with a high volume of inventory movement. However, certain businesses with low-volume, high-value goods like car dealerships and art galleries may prefer the low cost and simplicity of a periodic inventory system.
Advantages of perpetual inventory
Here are some of the principal advantages of a perpetual inventory system:
1. It allows you to see data in real-time
With an advanced inventory management system you will have the most accurate information possible. And all in real-time. For instance, Brightpearl’s integrated inventory management system.
You can track accounts receivable for your warehouse or sales orders being processed in your fulfillment centers. And when returns are processed, the suitable stock will be available for resale almost instantaneously.
2. Improves inventory accuracy & helps avoid stock-outs
By using a perpetual inventory system, you will benefit from better inventory accuracy. This means that there’s less confusion and disappointment for your customers.
With Brightpearl’s inventory management solution, you can keep up-to-date on all of your products with the Replenishment report. You can create purchase orders in one click. You’ll stay on top of your most popular items and never miss a sale. And, you’ll have more accurate inventory numbers for all of your accounting records.
3. It saves you money
With Brightpearl, you can take advantage of data-driven inventory demand planning for improved inventory control.
From the app dashboard, you can get a clear view of inventory levels, stock on hand, cost of inventory, and items on purchase. Advanced notifications will keep you aware of your best sellers that need to be reordered and which items are your most overstocked.
Various forecasting metrics, like seasonality and trends, will help you stock the most important items and minimize overstocking. This means your business has less cash tied up in inventory that can be spent elsewhere.
And, of course, with real-time stock updates and tracking, your business can spend less on labor costs by performing minimal physical inventory accounting.
Disadvantages of perpetual inventory systems
The perpetual inventory system has plenty of benefits, but it isn’t perfect. There are a few drawbacks, which we’ll detail below—but overall, the advantages outweigh these disadvantages.
Theft
In a perpetual inventory system, stocktaking is done automatically through digital technology, based on real-time data from sales and purchases. Although warehouse staff will be scanning the items, the lack of a traditional physical inventory count can mean things are overlooked—accidentally or otherwise.
For example, a full shipment of Christmas items is received from the supplier, in good time for the holiday season. The items are scanned and added to the online product catalog. But while they’re on the warehouse shelves, an employee decides to steal some of them. Unless there’s a physical inventory count in the meantime, the discrepancy may go unnoticed until customers start ordering the items—and the picker discovers the box is almost empty.
In the periodic system, employees carrying out a cycle count would be checked before leaving the warehouse to ensure they hadn’t pocketed any of the goods.
Scanning issues
A perpetual inventory system requires items to be tagged so that they can be read by a barcode or RFID scanner. You need to factor in the time it will take to do this, plus the cost of the hardware—although many inventory management systems allow any mobile device to be used as a scanner.
Although digital tech means greater accuracy in general, errors may still occur if someone scans the wrong product. Employees need to be fully trained in the use of these devices. The other issue is that the technology itself could go wrong, caused by a glitch in the scanning system or in the wider inventory management software. Make sure you choose a secure and reliable solution.
Risk of damage to items
This is similar to the problem of theft. Let’s say an employee drops a breakable item, but is afraid to admit it. They quietly sweep away the broken pieces, but they don’t adjust the system to record the loss of this unit. Without a physical inventory count, you’ll go on believing that the warehouse has a full complement of the items, which will lead to you selling a product that doesn’t actually exist.
In addition, a physical count can be more suitable for perishable goods. You’ll have proper storage facilities in place for these items, and the system will record that they were put away in the correct place. But if you don’t physically check them, you may not spot a problem with the refrigeration system, and the items could spoil before anyone realizes.
How does a perpetual inventory system work?
A perpetual inventory system is the sensible choice for large enterprises and small businesses alike. Let’s go through the process to understand how everything works.
1. Inventory gets sold
When an item is purchased by a customer, that item is scanned by a team member at the point-of-sale (POS). The POS system then updates your account and debits the item from the inventory journal. This happens automatically in the case of an online transaction.
2. Real-time COGS updates
You can calculate your COGS with either the Last in, First Out (LIFO) accounting method or the First In, First Out (FIFO) accounting system. The former costs items based on the most recent purchase price. The latter costs items based on the oldest purchase price. As soon as an item is sold or received, your COGS is updated automatically.
3. Automatic reorder point calibration
Once you start using your perpetual inventory system, it only gets better with time. With more historical data, the system continually adjusts reorder points to optimize stock levels.
4. Purchase order generation
When an item you carry reaches the calculated reorder point, a purchase order is automatically generated by the system. The order is sent to your suppliers so you and your team can be worry-free about running out of inventory.
5. Receivables are scanned
Once your suppliers receive a purchase order, they will ship to your warehouse or fulfillment center.
When your team receives the order, they scan the items, and your warehouse management system will automatically credit them back onto your inventory journal. The items are now available to be sold, returned, transferred, and more.
6. No beginning or ending
The cycle then goes on and on. With more data, your perpetual inventory system becomes better at optimizing the automation process.
Perpetual inventory system formulas
In a perpetual inventory system, there are several formulas that will help you decide when to order more inventory and how much, as well as figuring out lead time and safety stock numbers:
EOQ
Economic Order Quantity (EOQ) considers how much it costs to store the goods, alongside the actual cost of the goods. You can then determine the optimal amount of inventory to buy in order to minimize expenses.
EOQ = √ 2 X (demand in units X order costs per purchase) / carrying costs per unit
COGS
When you sell products in a perpetual inventory system, the expense account increases and grows the costs of sales or cost of goods sold (COGS). These are the direct expenses from the production of goods during a period, not counting any distribution or sales costs. In a perpetual system, COGS is recorded after each sale, but you can calculate it for a period using this formula:
COGS = Beginning inventory + Purchases – Ending inventory
Gross Profit Method
You can use COGS to calculate the gross profit, which is the product revenue minus COGS. You might have to make an estimate of the final inventory for a particular period while preparing accounting documents and statements.
Gross profit = Revenue – COGS
WAC
Weighted Average Cost is the cost flow assumption used to value your inventory. It’s the average COGS for all the inventory. In a perpetual system, you can use WAC to calculate an average unit cost, COGS for a period, and ending inventory for a period.
In a perpetual WAC calculation, the software recalculates the unit cost after every purchase, showing the current balance of units in stock and the average of their prices. The next sales transaction reflects this newly calculated unit cost.
Periodic and perpetual inventory system example
We’ve covered the way both these systems work, but here’s a further example of the difference between periodic and perpetual inventory systems.
In a periodic inventory system, the beginning and ending inventory is physically counted at each end of a given period. The company will also account for total purchases made for inventory in that period, to determine the cost of goods available for sale.
Cost of Goods Available for Sale = Beginning Inventory + Purchases
If your beginning inventory was worth $20,000, and you made $4,000 of purchases during the period, the cost of goods available for sale would be $24,000.
To work out the COGS, we need the ending inventory balance, which is £17,000.
COGS = Cost of Goods Available for Sale – Ending Inventory.
$24,000 – £17,000 = $7,000
A perpetual inventory management system tracks each transaction in real-time, meaning that all received inventory is instantly added to the database via barcode scanners. By default, all merchandise sold is eliminated to compute the Cost of Goods Sold (COGS) immediately.
Perpetual inventory system best practices
Categorize your Inventory
As you begin to implement your new perpetual inventory method, make sure to listen to the early information you receive. Segment your products into bestsellers, average-sellers, and low-demand stock. In this way, you will be able to invest your capital more efficiently and hone in on optimal reorder points. Your business will be able to fine-tune the amount of inventory and adjust to developing trends over time.
Optimize your warehouse layout
Image source: Unsplash
With advanced forecasting from Brightpearl’s inventory management software, you can make better decisions on your warehouse floor plan.
Keep your top-selling items closer to your packing stations, and less frequent purchases further out. Make use of barcode scanners or an RFID tracking system to have insurance against potential human error.
Stop overstocking and understocking!
Any items that are slow movers are costing you money and taking up space in your warehouse that could be used for your money makers. And when your products stock out, you are at risk of losing a sale or even lowering customer loyalty.
Use your real-time tracking to get accurate inventory information and achieve inventory balance as soon as possible. With accurate inventory details, you can tweak pricing, marketing, and more, to help achieve the best results.
Rotate stock
For medium and slow-moving product lines, make sure the oldest products are the first ones to leave the warehouse. Make sure all staff know to give the oldest items priority when it comes to packing orders.
You can ensure this by tracking LOT or serial numbers. Doing this goes hand-in-hand with choosing the FIFO (first in, first out) costing method over the LIFO (last in, last out) option.
Optimize reorder points
Yes, a perpetual inventory management system will let you know when stock is low. But someone has to be either monitoring the inventory account or notifications need to be turned on.
Use tools like Brightpearl’s inventory reports to determine optimal reorder points for your most important products. Automate as much of the reorder process as possible to minimize human error.
By using an inventory management platform like Brightpearl, you get real-time inventory updates. And when combined with barcode scanning technology, you can set automated reorder points. This means your team saves valuable time and you will never run out of important stock.
Automate, Automate, Automate
Speaking of automation, make sure you use a top platform like Brightpearl so that you can automate as much of the mundane and time-consuming work as possible. In addition to eliminating stock outs with automatic reorder points you can also automate:
- Inventory level updates with barcode scanning
- Accounting adjustments
- Real-time FIFO valuation
- Order fulfillment with integrated shipping management
- Customized product bundles with inventory adjustment
- And much more!
Use an inventory management system to make your team’s job easier and save them time to focus on the important things. Let Brightpearl handle the rest!
Training and education
Technology has given us the tools to automate many of the mundane tasks of an inventory system. It saves time and money that can be invested in more important areas of the business. But its data is only as accurate as the humans using it. That’s why it’s important to provide ample training and learning resources to all relevant team members.
Brightpearl Training can provide in-depth online or in-person guidance. The training sessions are tailored to what your business needs and how it operates.
There are flexible options, so every staff member can move through the onboarding process as convenient. Don’t take any chances and ensure proper implementation of your perpetual inventory system.